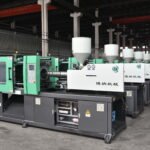
Solution 001
23 September, 2024In the field of plastic product production, the injection molding machine is the core equipment, and its performance directly affects product quality, production efficiency, and enterprise economic benefits. Therefore, it is crucial to correctly select the appropriate injection molding machine. This article will provide you with professional selection guidance from multiple key dimensions.
I. Clarify Production Requirements
After – sales Service
A complete after – sales service system is an important factor that cannot be ignored when choosing an injection molding machine. Ensure that the supplier can provide timely technical support, spare parts supply, and equipment maintenance services to reduce equipment downtime and ensure the continuity of production.
V. Budget Considerations
On the premise of meeting production requirements, formulate a reasonable budget in combination with the enterprise’s financial situation. It is necessary to avoid choosing an injection molding machine with poor quality and performance due to the pursuit of low prices, which affects production and product quality; nor should one blindly pursue high – end equipment, resulting in waste of funds. It is necessary to comprehensively weigh the cost – performance ratio of the equipment and select the injection molding machine that is most suitable for the enterprise.
Correctly selecting the appropriate injection molding machine requires comprehensive and meticulous consideration of the above – mentioned factors. Only in this way can an injection molding machine with excellent performance, meeting production requirements, and high cost – performance ratio be selected, providing a strong guarantee for the plastic product production of enterprises and enhancing the market competitiveness of enterprises.
Product Dimensions and Weight
Accurately measure the length, width, height, and weight of plastic products, and determine the clamping force and injection volume of the injection molding machine based on these data. If the product is large in size and heavy in weight, an injection molding machine with a large clamping force and a large injection volume is required; conversely, a smaller – sized device can be selected. For example, when producing large – sized plastic barrels, an injection molding machine with a large clamping force and a large injection volume needs to be equipped to ensure that the plastic melt can fill the mold cavity and guarantee the molding quality.
Product Precision Requirements
Different plastic products have significantly different precision requirements. For example, the outer shells of precision electronic components have strict dimensional tolerance requirements, and an injection molding machine with high injection precision and good control performance must be selected to ensure the dimensional stability of the products and meet the high – precision production requirements.
II. Consider the Type of Injection Molding Machine
Screw – type Injection Molding Machine
With the advantages of uniform plasticization, strong plasticization ability, and easy control of injection pressure and speed, it is widely used in the injection molding field, especially suitable for processing thermoplastic plastics, such as common polyethylene, polypropylene, polystyrene, etc.
Plunger – type Injection Molding Machine
It has a relatively simple structure, but the plasticization effect is not ideal. It is only suitable for processing plastics with good fluidity and low requirements for plasticization, such as some soft plastic products.
III. Pay Attention to Key Parameters
Clamping Force
The clamping force should be greater than the mold – opening force generated by the plastic melt on the mold cavity during the injection molding process. Otherwise, it will cause problems such as the mold opening and flash on the product. The calculation formula is: Clamping force = the projected area of the product on the parting surface × cavity pressure. When actually selecting, a certain safety factor needs to be considered.
Injection Volume
The injection volume should meet the weight requirements of plastic products. Generally, the theoretical injection volume of the injection molding machine should be 1.2 – 1.5 times greater than the weight of the product to ensure the smooth completion of the injection process.
Injection Pressure
The injection pressure needs to be determined according to factors such as the fluidity of the plastic, the complexity of the product, and the wall thickness. For products with poor fluidity, complex structures, or thin wall thicknesses, a higher injection pressure is required.
Injection Speed
The injection speed affects the molding quality and production efficiency of the product. For thin – walled products, a faster injection speed is required to avoid insufficient filling due to the rapid cooling of the melt in the cavity; for thick – walled products, the injection speed can be appropriately reduced to prevent problems such as jetting and air entrapment.
IV. Evaluate Brand and After – sales Service
Brand Reputation
Give priority to choosing injection molding machine brands with high market popularity and good reputation. These brands usually have advantages in product quality, technology research and development, and production processes, and the stability and reliability of the equipment are more guaranteed.